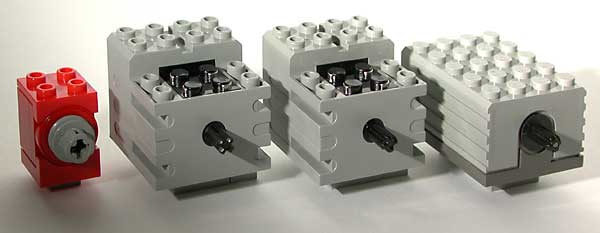
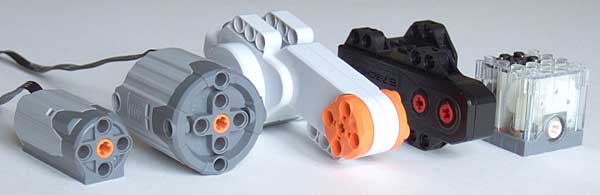

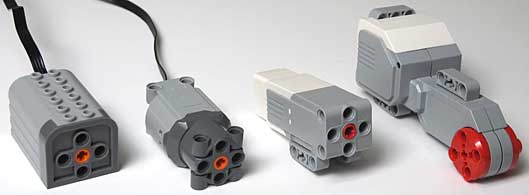
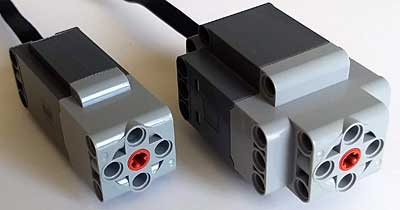
See also this comparison
page.
Thomas Avery has also performed measures on
5292 motors, see Lugnet
thread.
The roster
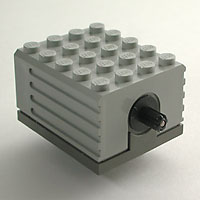
|
Electric Technic Motor 9V
Lugnet
Partsref 2838c01, Peeron
2838c01, Lego 74569
The older 9V Technic motor (1990).
Ungeared, it has a high rotation speed and low torque,
so for most applications it requires an external
gear reduction. |
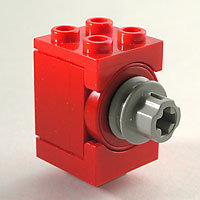
|
Electric Technic Micromotor
Lugnet
Partsref 2986, Peeron
2986, Lego 70823
Appeared in 1993, this small, light
weight motor turns slowly and offer low torque -
but respectable torque for its size. Must be used
generally with pulley,
top
and base,
but other motion transmissions are possible (see
examples by Brian Sadowsky, with a 16t
gear/clutch or a pin
joiner) |
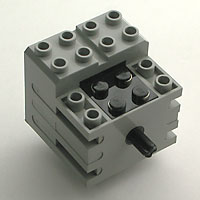
|
Electric Technic Mini-Motor 9v
Lugnet
Partsref 71427c01, Peeron
71427c01, Lego 71427
Since 1997, this motor replaces
2838. Geared down and quite efficient, this is the
motor of choice for most applications. |
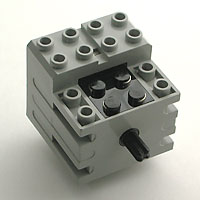
|
Electric Technic Mini-Motor 9v
Lego 43362
In 2002, Lego replaced 71427 motor
with a new type, 43362. Externally almost identical,
its internal structure is
very different. Performances are almost as good,
and its weight is much lower. |
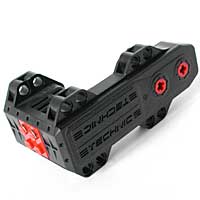
|
Electric RC Race Buggy Motor
Peeron
5292
(data
updated on Augus 15, 2012: some values were all
wrong!) Introduced in 2002, this
motor appeared with 8475
RC Race Buggy. Very powerful, it also consumes
a lot of energy. Not recommended for use with a
RCX which can't deliver the current needed by this
beast. The innermost shaft hole is geared up by
a 23/17 factor. Only the outermost output is tested
below. |
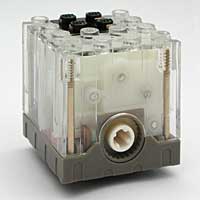
|
Electric Technic Motor 9V Geared
Peeron
47154
This motor was first included in
4094
Motor Movers set (2003). Provides an axle hole
with friction, allowing to choose axle length without
the need of an extender. Flat bottom allowing easy
mounting. |
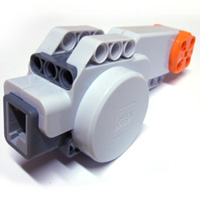
|
NXT motor
This motor is specific to the NXT
set (2006). Includes a rotation encoder, returning
to the NXT the position of the shaft with 1°
resolution. Because of the special connector of
this motor (non-standard phone plug type), a cable
adapter is required to drive this motor with regular
9V sources. Not recommended for use with a RCX which
can't deliver the high current that this motor can
consume. Slow rotation speed, minimizing the need
of external gear train. |
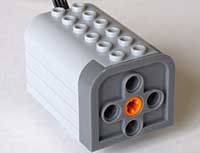
|
Power Functions E-motor
Introduced with LEGO Education |
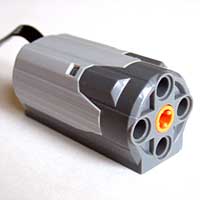
|
Power Functions Medium motor
This motor belongs to a new range
of motors and control elements introduced in 2007,
the Power Functions. It uses a new 4 pins 9V connector
that provides permanent 9V supply to control elements
as well as controlled power to the motors (compatibility
with old 9V system is built in extension cords).
The Medium motor has holes for studless constructions
as well as 6x2 bottom plate. |
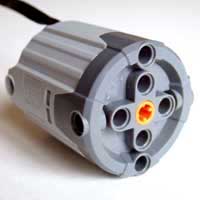
|
Power Functions XL motor
Big brother of Power Functions Medium
motor, it provides a lot of mechanical power. Actuated
by the same core as NXT motors, it rotates slightly
faster (less internal gear reduction). Mounting
is done through several pin holes. |
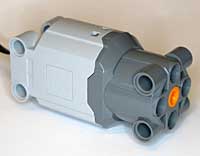
|
Power Functions Large motor
This motor appeared first in Rock
Crawler set (9398). Significantly more powerful
than the medium motor, it packs a lot of power in
a light, small package with many convenient mounting
options. But it's efficiency at light load is pretty
low (large current at no-load). |
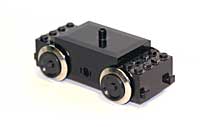
|
9V Train motor
Stefan Vorst measured performances
of the 9V Train motor. The results are below. |
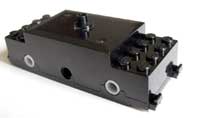
|
RC Train motor
This motor was introduced when LEGO
stopped the 9V train with metal tracks. The performances
of this motor are... not so good. |
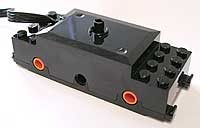
|
Power Functions Train motor
As the train system unifies with
Power Functions, this motor, equipped with a PF
cable and connector, replaces the RC train motor.
Fortunately the performances are much improved,
with an efficiency and power even exceeding the
old 9V train motors. |
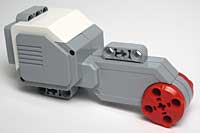
|
EV3 Large motor
This motor is very similar to NXT
motor, but with slightly better fixing capability
(compatible with Technic frames, holes aligned with
hub). Its efficiency seems slightly lower. |
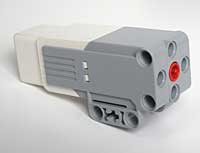
|
EV3 Medium motor
This motor is one of the highlights
of EV3 set compared to NXT one: a motor of reduced
size and classical front axle hub. Reduced size
comes with reduced power, similar to PF medium motor
(but being more down-geared, it is slower and delivers
more torque). |
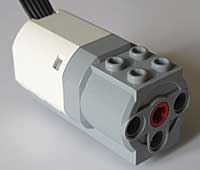
|
Powered Up Medium
This one is the evolution of PF-Medium
motor, but with the LPF2 / Powered Up connector.
It has very similar characteristics as its predecessor.
One less Technic pin hole on front, but studs on
top... |
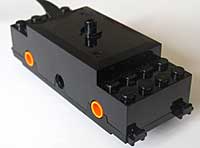
|
Powered Up Train motor
This is the new version of train
motor, but with the new LPF2 / Powered Up connector.
It has very similar characteristics as its predecessor.
My measurements shows a higher internal friction
(increased current/lower maximum speed) but this
is probably caused by individual variation (tested
on one sample only) |
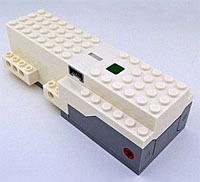
|
Boost Internal motor
I was able to open my move hub and
test the internal motor. This one is rather powerful,
but no load current is pretty high! |
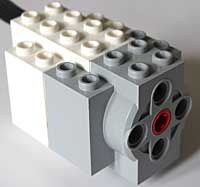
|
Boost External motor
This motor comes with the Boost
set and uses LPF2 connector. Mechanical power is
a bit lower than Powered Up Medium, but more internal
down gearing allow to get a slightly higher torque.
But the main difference is that this motor includes
a rotation encoder with 1° resolution. |
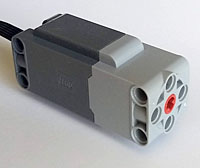
|
Control+ L motor The
new Control+ large motor, successor of PF large
motor with LPF2 connector, share the same drawback:
a high no-load current, thus relatively low efficiency.
But it delivers more power, and since it has a higher
gearing down ratio, the available torque is significantly
higher. It also includes a rotation encoder with
1° resolution and an absolute encoder. But since
there is no outside indication of 0 position, you
must do some guesswork to know the quadrant the
shaft currently is. |
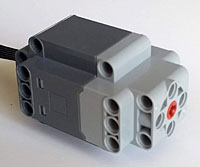
|
Control+ XL motor Replacement
of the Power Functions XL motor with LPF2 connector,
C+ XL is a bit more bulky, but features a lot of
convenient mounting points (it also include the
same rotation/angle sensors as C+ large motor).
But I am puzzled by this one: its rotation speed
and delivered power are so similar to those of C+
large motor that I don't see the point of this more
bulky version! Only the no-load current/efficiency
are better. Maybe this one has a better reliability
at high torque? |
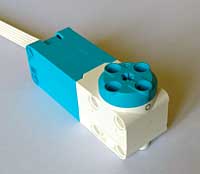
|
Spike Prime Medium motor This
motor was introduced with LEGO Education Spike Prime
robotics platform. The axle hub is perpendicular
to motor length like older NXT and EV3 motors. It
includes a rotation encoder with 1° resolution
and an absolute encoder and a mark allowing you
to know where the 0° angle is located. There
is a detailed official technical
specifications sheet, and though it is specified
at 7.2V (Spike Prime voltage), it matches pretty
well my measurements. This motor is not very powerful,
delivering less than 1W of mechanical power and
has a poor efficiency. The numerous attachment points
makes it very easy to build with. |
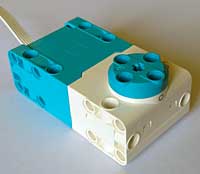
|
Spike Prime Large motor This
motor shares many characteristics of the medium
motor (rotation encoder, ease of building, availability
of technical
specifications sheet). It is much more powerful
than its medium sized companion (almost 2W of mechanical
power) but actual sustained power will be limited
by motor driver chip inside hub. Note that the internal
resettable fuse seems rated rather high, I was able
to use it for some time with a 900mA current. |
Weight
 2838
|
 2986
|
 71427
|
 43362
|
 5292
|
 47154
|
 NXT
|
 E-Motor
|
 PF Medium
|
 PF XL
|
 9V Train
|
 RC Train
|
48g |
10g |
42g |
28g |
55g |
40g |
80g |
50g |
31g |
69g |
72g |
53g |
 PF Train
|
 PF Large
|
 EV3 Large
|
 EV3 medium
|
 PUP Train
|
 PUP medium
|
 Boost Ext.
|
 Boost Int.
|
 Control+ L
|
 Control+ XL
|
 Spike M
|
 Spike L
|
57g |
42g |
82g |
39g |
57g |
34g |
43g |
- |
53g |
76g |
49g |
71g |
Supposed to be equivalent to 71427, 43362 motor is 30% lighter.
This is generally an advantage, except when the motor is used
as a counterweight, or to balance the structure, for example
in COG-shifting walkers.
No-load characteristics
Test conditions: motor is powered by a variable, regulated
power supply. An ammeter measures current flowing through the
motor, a voltmeter monitors tension across. The rotation speed
is measured by a RCX equipped with a light sensor, looking at
an half-white/half
black cylinder.
9 V supply |
 2838
|
 2986
|
 71427
|
 43362
|
 5292
|
 47154
|
 NXT
|
 E-Motor
|
 PF Medium
|
 PF XL
|
 9V Train
|
 RC Train
|
Rotation
speed (rotations per minute) |
4100 rpm |
35 rpm |
360 rpm |
340 rpm |
1700 rpm
/ 1240 rpm |
460 rpm |
170 rpm |
780rpm |
405 rpm |
220 rpm |
2000rpm |
2000rpm |
No-load current |
35 mA |
6 mA |
3.5 mA |
9 mA |
160 mA |
31 mA |
60 mA |
17.5mA |
65 mA |
80 mA |
90mA |
90mA |
9 V supply |
 PF Train
|
 PF Large
|
 EV3 Large
|
 EV3 Medium
|
 PUP Train
|
 PUP medium
|
 Boost Ext.
|
 Boost Int.
|
 Control+ L
|
 Control+ XL
|
 Spike M
|
 Spike L
|
Rotation
speed (rotations per minute) |
1900rpm |
390 rpm |
175rpm |
260 rpm |
1760 rpm |
380 rpm |
255 rpm |
350 rpm |
315 rpm |
330 rpm |
228 rpm |
213 rpm |
No-load current |
90mA |
120 mA |
60mA |
80 mA |
100 mA |
60 mA |
41 mA |
140 mA |
120 mA |
60 mA |
100 mA |
110 mA |
43362 has a higher no-load current than 71427, probably
caused by higher internal
friction. 47154 has a fairly high no-load current, because
of its 5-stages gear reduction. But it uses big-tooth gears
in the last stages, probably much more sturdy that the 2-stages,
thin-tooth 71427/43362 internal gearing. The 5292 also exhibit
very high no-load current, here again caused by internal friction.
This explains also the break in its speed/voltage curve. All
train motors show similar no-load characteristics, especially
a relatively high current.
As is usual for DC motors, rotation speed is proportional
to voltage applied to them, this can be seen on graphs below.
No-load current depends little on voltage.
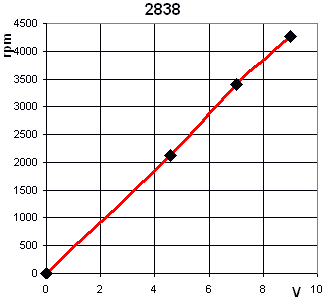
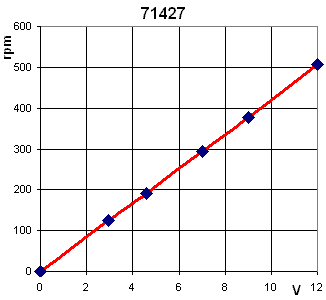
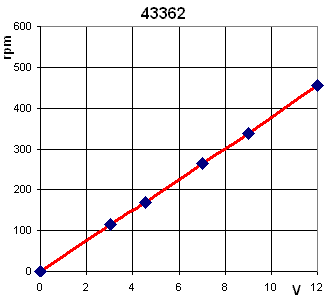
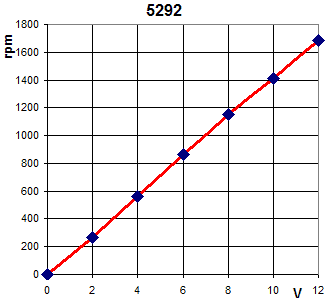
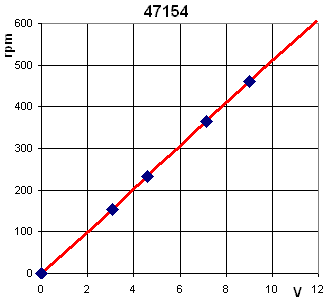
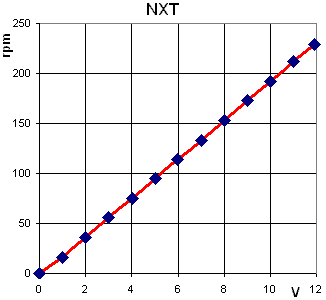
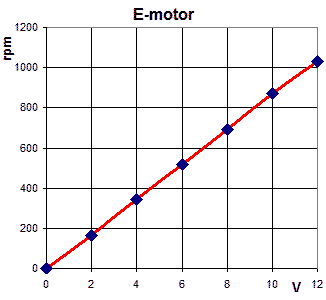
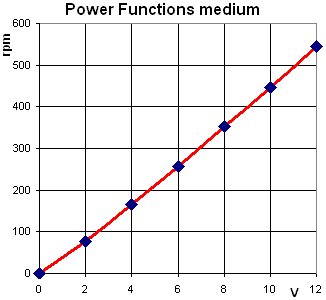
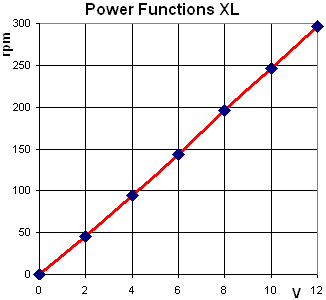
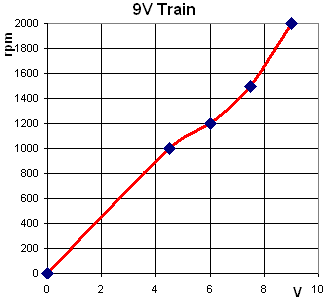
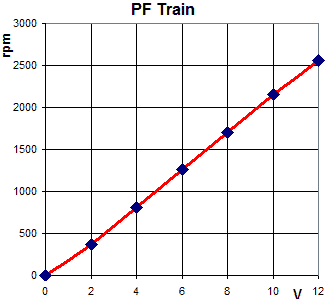
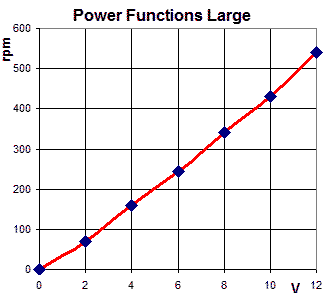
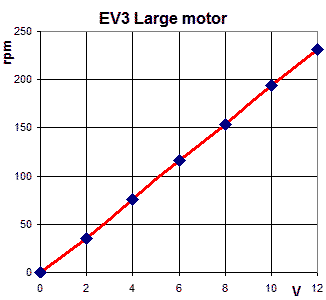
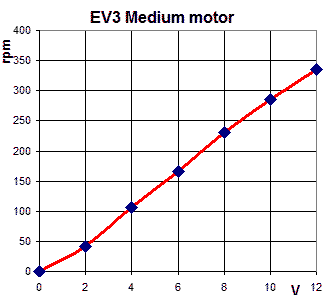

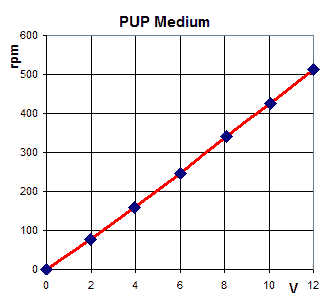
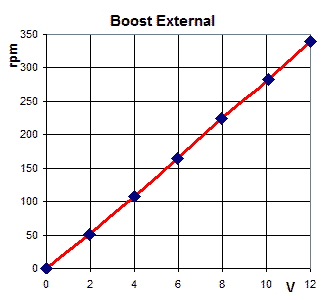
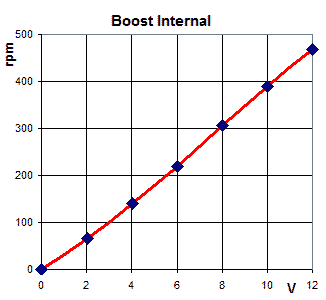
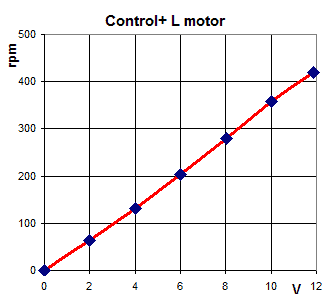
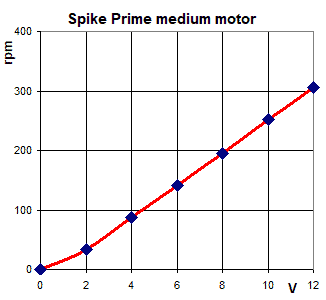
Stalled characteristics
Stalled current consumption is simply measured with motor
axle shaft locked by hand. Stalled torque is established from
the maximum weight that can be lifted by the machine described
below. Note that stalled torque value is VERY imprecise.
9 V supply |
 2838
|
 2986
|
 71427
|
 43362
|
 5292
|
 47154
|
 NXT
|
 E-Motor
|
 PF Medium
|
 PF XL
|
 9V Train
|
 RC Train
|
Stalled
torque |
0.85 N.cm |
1.6 N.cm |
6 N.cm |
5.5 N.cm |
14 N.cm |
6 N.cm |
50 N.cm |
3.4N.cm |
11 N.cm |
40 N.cm |
2.8 N.cm |
1.7 N.cm |
Stalled current |
700 mA |
80 mA |
360 mA |
340 mA |
3.2 A |
580 mA |
2 A |
410 mA |
850 mA |
1.8 A |
950 mA |
750 mA |
9 V supply |
 PF Train
|
 PF Large
|
 EV3 Large
|
 EV3 Medium
|
 PUP Train
|
 PUP medium
|
 Boost Ext.
|
 Boost Int.
|
 Control+ L
|
 Control+ XL
|
 Spike M
|
 Spike L
|
Stalled
torque |
3.6 N.cm * |
18 N.cm |
43 N.cm |
15 N.cm |
2.9 N.cm * |
11 N.cm ** |
9.5 N.cm ** |
15.8 N.cm |
26 N.cm *** |
22 N.cm *** |
13.5 N.cm |
33.5 N.cm |
Stalled current |
1.3 A * |
1.3 A |
1.8 A |
780 mA |
1.1 A * |
0.8 A
** |
450 mA ** |
1050 mA |
1.4 A
*** |
1.1 A *** |
0.85 A
|
1.8 A |
Take care to avoid extended period stall condition, as power
dissipated in motor case is quite high (6 Watts for 2838, 3
W for 71427) will cause a rapid temperature rise. Note that
71427 and 43362 motors, equipped
with a thermistor, should be protected against frying (not
tested though !!!). 5292 motor is protected too, since stalled
current decreases quickly (It's the rectangular yellow component
on this photo.
47154 protection can be seen easily through
clear case.
The NXT motor is also protected by a thermistor
(Raychem RXE065 or Bourns MF-R065).
That means that the high 2A current (and associated whooping
torque) can be sustained only for a few seconds. Same thing
for the Power Functions XL motor.
(*) The train motors also contain thermistor limitations.
For the PF train motor, this protection trips too fast and prevents
direct measure of the stalled current. These values were obtained
by extrapolation.
(**) Powered Up medium motor and Boost external motor have
fast tripping thermistor limitation, that seem to trip at a
fairly low current (around 400mA), that prevents direct measurement
of stall current and torque. These values are thus obtained
by extrapolation (and is not really meaningful for Powered Up
medium motor that can be feed only with half the stall current).
(***) Control+ motors stalled current was also obtained by
extrapolation.
Loaded characteristics
Here is the setup used to measure motors under load. Electrical
power is measured with voltmeter and ammeter. Mechanical power
delivered by the motor is evaluated from the time used to lift
the weight by some height (5 cylinder turns - the first two
turns are not counted to eliminate initial acceleration). Torque
applied is obtained from weight and cylinder radius.
Cylinder is directly placed on motor axle shaft, except for
2838 motor where a 1/5 gear reduction was used. Additionnal
friction introduced may have somewhat impacted 2838 efficiency,
but anyway this gearing is necessary for most applications.
Torque displayed for this motor corrects gear reduction. The
fast 5292 motor, the PF and RC train motors were also measured
with a 1/3 gear reduction.
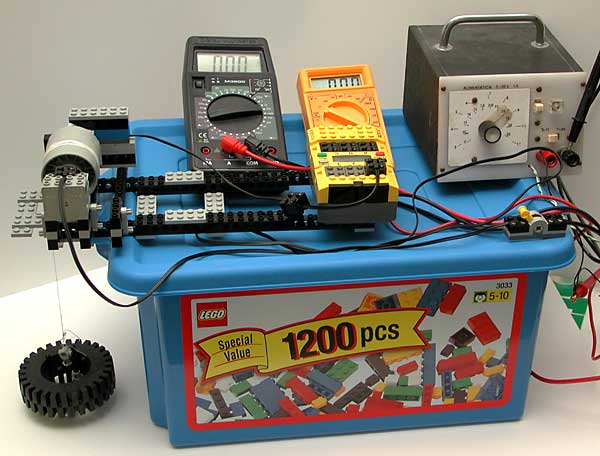
In 2010 I updated my test
setup to the NXT platform: Mindsensors
launched the PowerMeter
sensor that allows the NXT to measure directly the voltage
applied to the motor and the current consumed. A light sensor
in front of a black and white cylinder reads the number of turns
done by the winch, and the time needed to lift the weight. Using
custom board with two electromechanical relays, the NXT can
control the motor under test: run, float or brake (this later
state is used to prevent the load to drop brutally on the floor
at the end of lifting). A laboratory power supply is used to
power the motor under test.
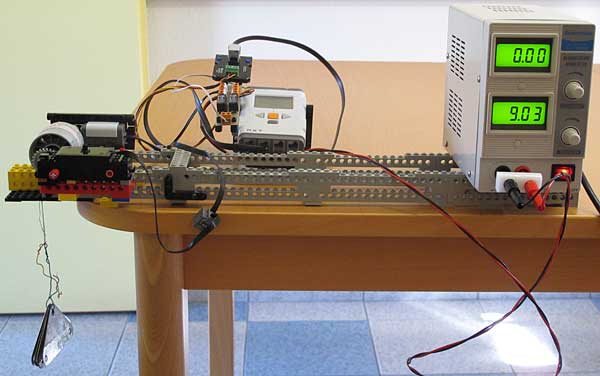
The photo below shows the NXT equipped with
PowerMeter
sensor and motor control board.
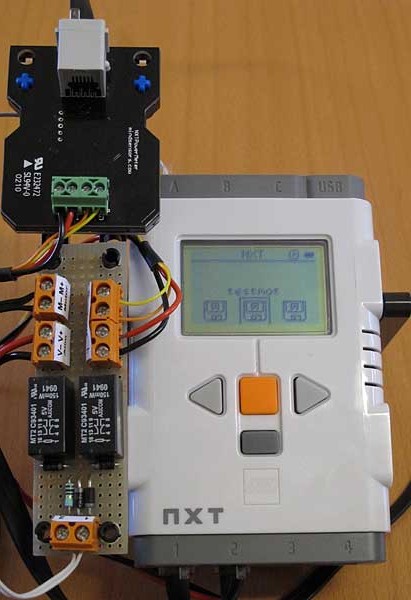
Here is a screen capture of the NXC
motor test program:
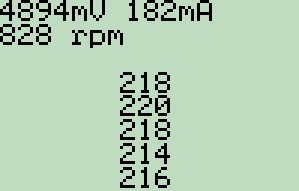
 2838
|
Torque |
Rotation
speed |
Current |
Mechanical power |
Electrical power |
Efficiency |
6
V |
0.45
N.cm |
580
rpm |
0.32
A |
0.27
W |
1.9
W |
14
% |
7
V |
0.45
N.cm |
1000
rpm |
0.32
A |
0.46
W |
2.3
W |
20
% |
9
V |
0.45
N.cm |
2000
rpm |
0.32
A |
0.9
W |
3
W |
31
% |
12
V |
0.45
N.cm |
3300
rpm |
0.33
A |
1.5
W |
4
W |
39
% |
|
 71427
|
Torque |
Rotation
speed |
Current |
Mechanical power |
Electrical power |
Efficiency |
4.5
V |
2.25
N.cm |
57
rpm |
0.12
A |
0.13
W |
0.54
W |
24
% |
7
V |
2.25
N.cm |
160
rpm |
0.12
A |
0.38
W |
0.85
W |
45
% |
9
V |
2.25
N.cm |
250
rpm |
0.12
A |
0.58
W |
1.1
W |
54
% |
12
V |
2.25
N.cm |
375
rpm |
0.12
A |
0.88W |
1.5
W |
61
% |
|
 43362
|
Torque |
Rotation
speed |
Current |
Mechanical power |
Electrical power |
Efficiency |
4.5
V |
2.25
N.cm |
50
rpm |
0.12
A |
0.12
W |
0.54
W |
22
% |
7
V |
2.25
N.cm |
140
rpm |
0.12
A |
0.33
W |
0.85
W |
39
% |
9
V |
2.25
N.cm |
219
rpm |
0.12
A |
0.51
W |
1.1
W |
47
% |
12
V |
2.25
N.cm |
333
rpm |
0.12
A |
0.77W |
1.5
W |
54
% |
|
 47154
|
Torque |
Rotation
speed |
Current |
Mechanical power |
Electrical power |
Efficiency |
4.5
V |
2.25
N.cm |
90
rpm |
0.19
A |
0.21
W |
0.85
W |
24
% |
7
V |
2.25
N.cm |
210
rpm |
0.19
A |
0.49
W |
1.33
W |
37
% |
9
V |
2.25
N.cm |
315
rpm |
0.19
A |
0.74
W |
1.7
W |
43
% |
12
V |
2.25
N.cm |
468
rpm |
0.19
A |
1.1
W |
2.3
W |
48
% |
|
 2986
|
Torque |
Rotation
speed |
Current |
Mechanical power |
Electrical power |
Efficiency |
9
V |
1.28
N.cm |
16
rpm |
0.04
A |
0.021
W |
0.36
W |
16
% |
12
V |
1.28
N.cm |
28
rpm |
0.04
A |
0.038W |
0.48
W |
28
% |
|
 5292
|
Torque |
Rotation
speed |
Current |
Mechanical power |
Electrical power |
Efficiency |
4.5
V |
5.7
N.cm |
150
rpm |
1.36
A |
0.87
W |
6.12
W |
14
% |
6
V |
5.7
N.cm |
380
rpm |
1.38
A |
2.27
W |
8.28
W |
27
% |
7.5
V |
5.7
N.cm |
580
rpm |
1.37
A |
3.45
W |
10.3
W |
34
% |
9
V |
5.7
N.cm |
780
rpm |
1.40
A |
4.61
W |
12.6
W |
37
% |
10.5
V |
5.7
N.cm |
1030
rpm |
1.46A |
6.16
W |
15.3
W |
40
% |
|
 NXT
|
Torque |
Rotation
speed |
Current |
Mechanical power |
Electrical power |
Efficiency |
4.5
V |
16.7
N.cm |
33
rpm |
0.6
A |
0.58
W |
2.7
W |
21.4
% |
7
V |
16.7
N.cm |
82
rpm |
0.55
A |
1.44
W |
3.85
W |
37.3
% |
9
V |
16.7
N.cm |
117
rpm |
0.55
A |
2.03
W |
4.95
W |
41
% |
12
V |
16.7
N.cm |
177
rpm |
0.58
A |
3.10
W |
6.96
W |
44.5
% |
|
 PF Medium
|
Torque |
Rotation
speed |
Current |
Mechanical power |
Electrical power |
Efficiency |
4.5
V |
3.63
N.cm |
73
rpm |
0.28
A |
0.27
W |
1.26
W |
22
% |
7
V |
3.63
N.cm |
185
rpm |
0.29
A |
0.70
W |
2.03
W |
34
% |
9
V |
3.63
N.cm |
275
rpm |
0.31
A |
1.04
W |
2.79
W |
37
% |
12
V |
3.63
N.cm |
405
rpm |
0.32
A |
1.53
W |
3.84
W |
40
% |
|
 PF XL
|
Torque |
Rotation
speed |
Current |
Mechanical power |
Electrical power |
Efficiency |
4.5
V |
14.5
N.cm |
43
rpm |
0.52
A |
0.65
W |
2.34
W |
28
% |
7
V |
14.5
N.cm |
100
rpm |
0.54
A |
1.51
W |
3.78
W |
40
% |
9
V |
14.5
N.cm |
146
rpm |
0.55
A |
2.21
W |
4.95
W |
45
% |
12
V |
14.5
N.cm |
214
rpm |
0.56
A |
3.24
W |
6.72
W |
48
% |
|

9V Train
|
Torque |
Rotation
speed |
Current |
Mechanical power |
Electrical power |
Efficiency |
4.5
V |
0.90
N.cm |
375
rpm |
0.40
A |
0.36
W |
1.80
W |
20
% |
6
V |
0.90
N.cm |
667
rpm |
0.39
A |
0.62
W |
2.34
W |
27
% |
7.5
V |
0.90
N.cm |
1071
rpm |
0.38
A |
0.99
W |
2.85
W |
35
% |
9
V |
0.90
N.cm |
1250
rpm |
0.38
A |
1.11
W |
3.42
W |
33
% |
|

RC Train
|
Torque |
Rotation
speed |
Current |
Mechanical power |
Electrical power |
Efficiency |
3
V |
0.85
N.cm |
- |
- |
- |
- |
- |
4.5
V |
0.85
N.cm |
- |
- |
- |
- |
- |
6
V |
0.85
N.cm |
171
rpm |
0.43
A |
0.15
W |
2.59
W |
6
% |
7.5
V |
0.85
N.cm |
549
rpm |
0.43
A |
0.49
W |
3.23
W |
15
% |
9
V |
0.85
N.cm |
990
rpm |
0.43
A |
0.88
W |
3.91
W |
22
% |
10.5V |
0.85
N.cm |
1323
rpm |
0.44
A |
1.18
W |
4.63
W |
25
% |
12
V |
0.85
N.cm |
1683
rpm |
0.45
A |
1.50
W |
5.43
W |
27
% |
|

PF Train
|
Torque |
Rotation
speed |
Current |
Mechanical power |
Electrical power |
Efficiency |
3
V |
0.85
N.cm |
135
rpm |
0.35
A |
0.12
W |
1.05
W |
11% |
4.5V |
0.85
N.cm |
468
rpm |
0.36
A |
0.42
W |
1.62
W |
26
% |
6
V |
0.85
N.cm |
792
rpm |
0.37
A |
0.71
W |
2.22
W |
32
% |
7.5
V |
0.85
N.cm |
1107
rpm |
0.38
A |
0.99
W |
2.85
W |
35
% |
9
V |
0.85
N.cm |
1458
rpm |
0.38
A |
1.30
W |
3.42
W |
38
% |
10.5V |
0.85
N.cm |
1782
rpm |
0.39
A |
1.59
W |
4.10
W |
39
% |
12
V |
0.85
N.cm |
2124
rpm |
0.40
A |
1.90
W |
4.80
W |
40
% |
|

E-Motor
|
Torque |
Rotation
speed |
Current |
Mechanical power |
Electrical power |
Efficiency |
4.5V |
1.32
N.cm |
63
rpm |
0.17
A |
0.087
W |
0.76
W |
11
% |
6
V |
1.32
N.cm |
186
rpm |
0.17
A |
0.26
W |
1.02
W |
25
% |
7.5
V |
1.32
N.cm |
300
rpm |
0.17
A |
0.42
W |
1.27
W |
33
% |
9
V |
1.32
N.cm |
420
rpm |
0.18
A |
0.58
W |
1.62
W |
36
% |
10.5V |
1.32
N.cm |
520
rpm |
0.18
A |
0.72
W |
1.89
W |
38
% |
12
V |
1.32
N.cm |
640
rpm |
0.18
A |
0.89
W |
2.16
W |
41
% |
|

PF-large
|
Torque |
Rotation
speed |
Current |
Mechanical power |
Electrical power |
Efficiency |
4.5V |
6.48
N.cm |
67
rpm |
0.46
A |
0.46
W |
2.07
W |
22
% |
6
V |
6.48
N.cm |
138
rpm |
0.47
A |
0.94
W |
2.82
W |
33
% |
7.5
V |
6.48
N.cm |
203
rpm |
0.48
A |
1.38
W |
3.60
W |
38
% |
9
V |
6.48
N.cm |
272
rpm |
0.49
A |
1.85
W |
4.41
W |
42
% |
10.5V |
6.48
N.cm |
338
rpm |
0.49
A |
2.30
W |
5.15
W |
44
% |
12
V |
6.48
N.cm |
405
rpm |
0.50
A |
2.75
W |
6.00
W |
46
% |
|
 EV3 large
|
Torque |
Rotation
speed |
Current |
Mechanical power |
Electrical power |
Efficiency |
4.5
V |
17.3
N.cm |
24
rpm |
0.69
A |
0.43
W |
3.10
W |
14
% |
6
V |
17.3
N.cm |
51
rpm |
0.69
A |
0.92
W |
4.14
W |
22
% |
7.5
V |
17.3
N.cm |
78rpm |
0.69
A |
1.41
W |
5.17
W |
27
% |
9
V |
17.3
N.cm |
105
rpm |
0.69
A |
1.90
W |
6.21
W |
31
% |
10.5
V |
17.3
N.cm |
132
rpm |
0.69
A |
2.39
W |
7.24
W |
33
% |
12
V |
17.3
N.cm |
153
rpm |
0.69
A |
2.77
W |
8.28
W |
33
% |
|

EV3-medium
|
Torque |
Rotation
speed |
Current |
Mechanical power |
Electrical power |
Efficiency |
4.5V |
6.64
N.cm |
24
rpm |
0.35
A |
0.17
W |
1.57
W |
10
% |
6
V |
6.64
N.cm |
72
rpm |
0.35
A |
0.50
W |
2.10
W |
24
% |
7.5
V |
6.64
N.cm |
120
rpm |
0.35
A |
0.83
W |
2.62
W |
32
% |
9
V |
6.64
N.cm |
165
rpm |
0.37
A |
1.15
W |
3.33
W |
34
% |
10.5V |
6.64
N.cm |
207
rpm |
0.37
A |
1.44
W |
3.88
W |
37
% |
12
V |
6.64
N.cm |
249
rpm |
0.37
A |
1.73
W |
4.44
W |
39
% |
|
 PUP Train
|
Torque |
Rotation
speed |
Current |
Mechanical power |
Electrical power |
Efficiency |
4.5V |
0.88
N.cm |
237
rpm |
0.36
A |
0.22
W |
1.61
W |
13
% |
6
V |
0.88
N.cm |
540
rpm |
0.38
A |
0.50
W |
2.30
W |
22
% |
7.5
V |
0.88
N.cm |
855
rpm |
0.40
A |
0.79
W |
2.99
W |
26
% |
9
V |
0.88
N.cm |
1242
rpm |
0.41
A |
1.15
W |
3.73
W |
31
% |
10.5V |
0.88
N.cm |
1539
rpm |
0.43
A |
1.42
W |
4.50
W |
32
% |
12
V |
0.88
N.cm |
1872
rpm |
0.44
A |
1.73
W |
5.26
W |
33
% |
|

PUP medium
|
Torque |
Rotation
speed |
Current |
Mechanical power |
Electrical power |
Efficiency |
4.5V |
4.08
N.cm |
66
rpm |
0.29
A |
0.28
W |
1.29
W |
22
% |
6
V |
4.08
N.cm |
135
rpm |
0.29
A |
0.56
W |
1.73
W |
33
% |
7.5
V |
4.08
N.cm |
201
rpm |
0.30
A |
0.86
W |
2.22
W |
39
% |
9
V |
4.08
N.cm |
270
rpm |
0.30
A |
1.15
W |
2.66
W |
43
% |
10.5V |
4.08
N.cm |
327
rpm |
0.30
A |
1.40
W |
3.18
W |
44
% |
12
V |
4.08
N.cm |
396
rpm |
0.31
A |
1.69
W |
3.74
W |
45
% |
|

Boost Ext.
|
Torque |
Rotation
speed |
Current |
Mechanical power |
Electrical power |
Efficiency |
4.5V |
4.08
N.cm |
39
rpm |
0.18
A |
0.17
W |
0.82
W |
20
% |
6
V |
4.08
N.cm |
84
rpm |
0.18
A |
0.36
W |
1.09
W |
33
% |
7.5
V |
4.08
N.cm |
126
rpm |
0.19
A |
0.54
W |
1.43
W |
38
% |
9
V |
4.08
N.cm |
171
rpm |
0.19
A |
0.73
W |
1.72
W |
42
% |
10.5V |
4.08
N.cm |
213
rpm |
0.20
A |
0.93
W |
2.09
W |
44
% |
12
V |
4.08
N.cm |
255
rpm |
0.20
A |
1.09
W |
2.40
W |
45
% |
|
 Boost Int.
|
Torque |
Rotation
speed |
Current |
Mechanical power |
Electrical power |
Efficiency |
4.5V |
4.08
N.cm |
81
rpm |
0.33A |
0.35
W |
1.46
W |
24
% |
6
V |
4.08
N.cm |
141
rpm |
0.34
A |
0.60
W |
2.06
W |
29
% |
7.5
V |
4.08
N.cm |
201
rpm |
0.35
A |
0.86
W |
2.66
W |
32
% |
9
V |
4.08
N.cm |
264
rpm |
0.37
A |
1.13
W |
3.37
W |
33
% |
10.5V |
4.08
N.cm |
327
rpm |
0.38A |
1.40
W |
3.98
W |
35
% |
12
V |
4.08
N.cm |
384
rpm |
0.39
A |
1.64
W |
4.67
W |
35
% |
|
 Control+ L
|
Torque |
Rotation
speed |
Current |
Mechanical power |
Electrical power |
Efficiency |
4.5V |
8.81
N.cm |
36
rpm |
0.49
A |
0.33
W |
2.21
W |
15
% |
6
V |
8.81
N.cm |
93
rpm |
0.48
A |
0.86
W |
2.88
W |
30
% |
7.5
V |
8.81
N.cm |
141
rpm |
0.51
A |
1.30
W |
3.81
W |
34
% |
9
V |
8.81
N.cm |
198
rpm |
0.52
A |
1.83
W |
4.70
W |
39
% |
10.5V |
8.81
N.cm |
255
rpm |
0.52
A |
2.35
W |
5.44
W |
43
% |
12
V |
8.81
N.cm |
312
rpm |
0.53
A |
2.88
W |
6.37
W |
45
% |
|
 Control+ XL
|
Torque |
Rotation
speed |
Current |
Mechanical power |
Electrical power |
Efficiency |
4.5V |
8.81
N.cm |
33
rpm |
0.45
A |
0.30
W |
2.03
W |
15
% |
6
V |
8.81
N.cm |
93
rpm |
0.46
A |
0.86
W |
2.75
W |
31
% |
7.5
V |
8.81
N.cm |
147
rpm |
0.46
A |
1.36
W |
3.50
W |
39
% |
9
V |
8.81
N.cm |
198
rpm |
0.47
A |
1.83
W |
4.16
W |
44
% |
10.5V |
8.81
N.cm |
252
rpm |
0.47
A |
2.33
W |
4.95
W |
47
% |
12
V |
8.81
N.cm |
306
rpm |
0.47
A |
2.82
W |
5.70
W |
50
% |
|
 Spike M
|
Torque |
Rotation
speed |
Current |
Mechanical power |
Electrical power |
Efficiency |
4.5V |
4.48
N.cm |
24
rpm |
0.29
A |
0.11
W |
1.29
W |
9
% |
6
V |
4.48
N.cm |
63
rpm |
0.28
A |
0.30
W |
1.67
W |
18
% |
7.2
V |
3.5
N.cm |
135
rpm |
0.28A |
0.49
W |
2.02
W |
25
% |
7.5
V |
4.48
N.cm |
105
rpm |
0.29
A |
0.49
W |
2.16
W |
23
% |
9
V |
4.48
N.cm |
138
rpm |
0.30
A |
0.65
W |
2.67
W |
24
% |
10.5V |
4.48
N.cm |
180
rpm |
0.31
A |
0.84
W |
3.24
W |
26
% |
12
V |
4.48
N.cm |
213
rpm |
0.32
A |
1.00
W |
3.82
W |
26
% |
|
LEGO
technical specifications values |
|
 Spike L
|
Torque |
Rotation
speed |
Current |
Mechanical power |
Electrical power |
Efficiency |
4.5V |
8.47
N.cm |
48
rpm |
0.41
A |
0.43
W |
1.86
W |
23
% |
6
V |
8.47
N.cm |
84
rpm |
0.43
A |
0.75
W |
2.59
W |
29
% |
7.2
V |
8
N.cm |
135
rpm |
0.43
A |
1.13
W |
3.10
W |
37
% |
7.5
V |
8.47
N.cm |
126
rpm |
0.43
A |
1.12
W |
3.25
W |
34
% |
9
V |
8.47
N.cm |
156
rpm |
0.44
A |
1.38
W |
3.98
W |
35
% |
10.5V |
8.47
N.cm |
198
rpm |
0.46
A |
1.76
W |
4.82
W |
36
% |
12
V |
8.47
N.cm |
234
rpm |
0.46
A |
2.08
W |
5.47
W |
38
% |
|
LEGO
technical specifications values |
|
The speed of 43362 motor is about 12 % lower
than speed of 71427. Though this is in the range of variations
measured by Steve Baker among a bunch of nine
71427 motors, my measures on three 71427 and two 43362 showed
the 12 % difference between the two groups.
The RC train motor had a poor efficiency and delivers little
torque at low voltage (it was not able to move under 6V loaded
with 0.85 N.cm). The PF train motor has a much improved efficiency,
even better than the old 9V train motor.
Spike motor don't have an outstanding efficiency (Spike medium
motor fares quite bad in that respect. I quoted in yellow the
"official" values provided by LEGO Education in their
datasheets. As you can see the values match pretty well my measurements
(and no, I didn't have to adjust my figures to fit LEGO values
;) )
Speed and current vs.
torque
Curves showing rotation speed vs. torque and current consumed
vs. torque, both at nominal 9V voltage.
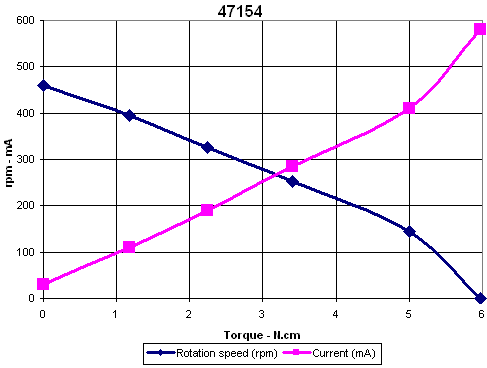
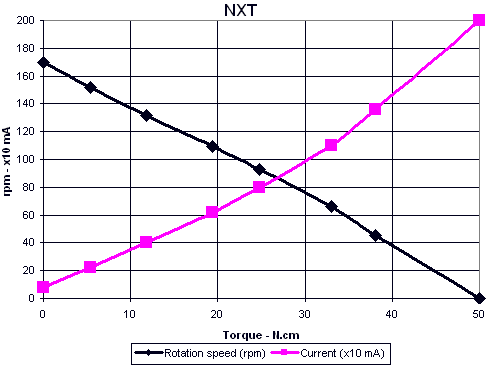
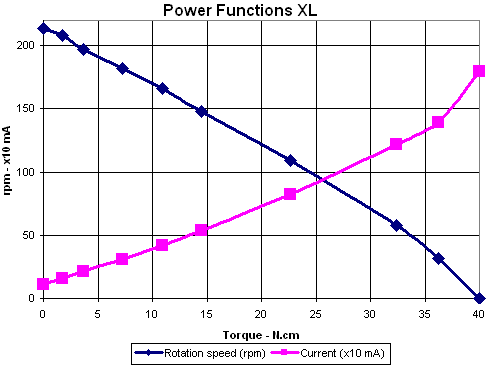
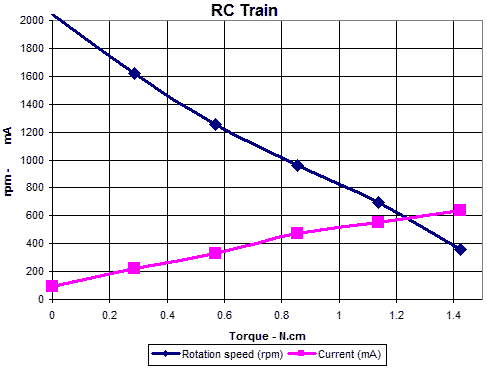
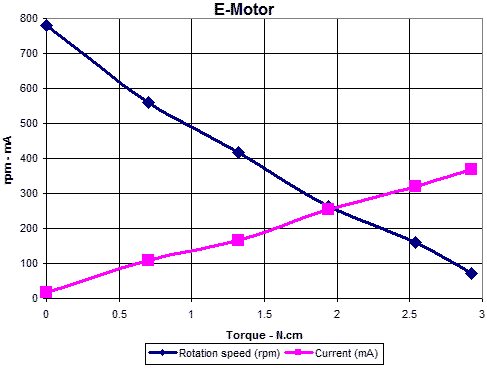
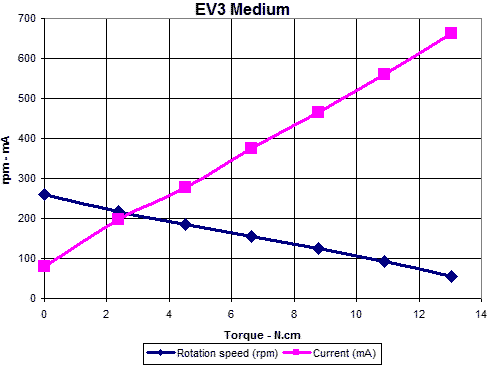
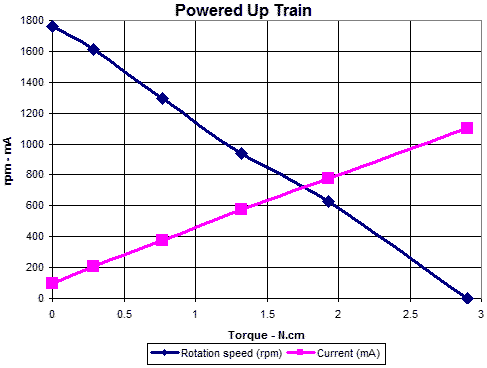
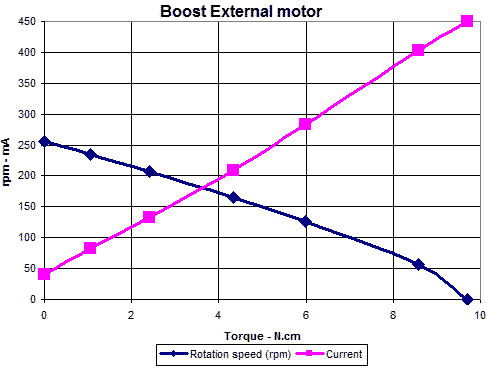
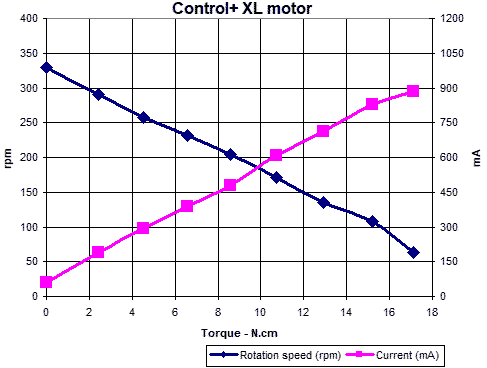
Synthesis
charts
These charts summarize the above curves. The most meaningful
shows the various motor sorted by maximum power they are able
to deliver at 9V. Because rpm/torque curve is linear a motor
provides maximum power when load slows it down to half of no-load
speed.
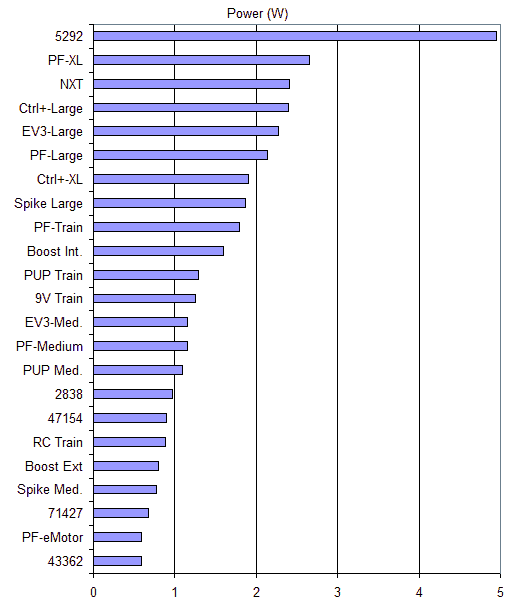
The following charts sort motors by torque and
by no-load rotation speed (of course this depends a lot on internal
down-gearing of the motors!!!). Torque chart lists torque at
half speed point.
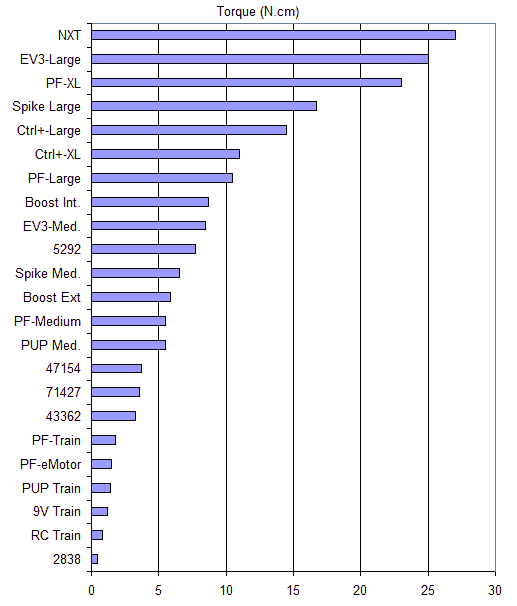
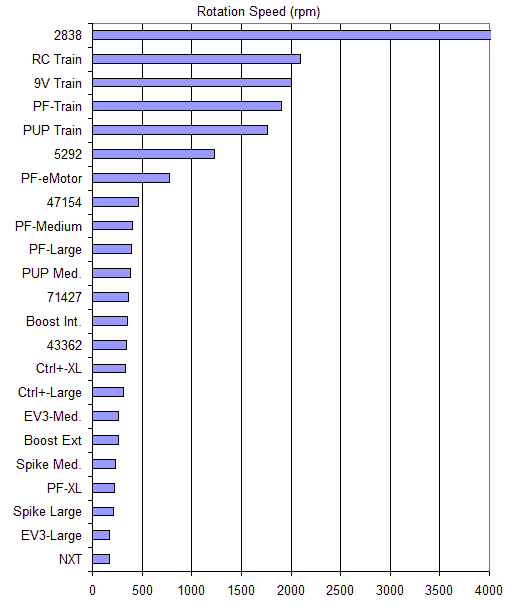
Protections
71427 and 43362 motors are protected from abuses by two devices:
- a PTC thermistance (here an Epcos
B1056). This resistor, mounted in series with the motor,
has a low value when it is cold (about 1.7 ohms), rapidly
increasing as temperature rises. When large current flows
through the motor, self heating rises thermistance temperature
and resistance value, so the current is limited by voltage
drop across thermistance.
- a BZW04-15B, bidirectional transient
voltage suppressor diode. This diode protects RCX from large
voltage spikes that could be generated by the motor. But
it also forbids applying more than 15V to the motor...
A similar protection is integrated in 47154 motors, as can
be seen on this photograph. NXT
motor is also protected with a PTC thermistance
and a transient voltage suppressor diode (D4 on this photograph).
Outputs of RCX are also protected from overload: the motor
driver chip used (Melexis MLX10402 - datasheet)
has a current limitation set to 500 mA, and a thermal shutdown
which disable the output if die temperature rises too much.
Here is the curve limitation that I measured on a RCX. It
was powered by an external regulated power supply, and tested
at 9V (6 alkaline batteries) and 7.2V (6 NiCd or NiMH rechargeable
batteries).
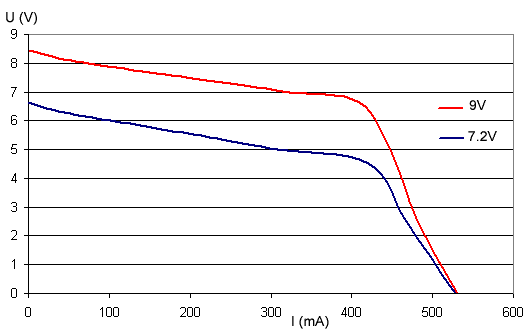
There is a significant voltage drop before reaching
current limitation knee (at about 500 mA). So a stalled 71427
motor receives only about 7V at 300 mA, while two paralleled
71427 or a single 2838 almost reach current limitation (5.5V
/ 430mA).
Once current limitation is established (for
example with a dead short), power dissipation in the driver
is very high, and it quickly enters thermal shutdown mode. After
that, the output cycles on/off with a period of about
1 second: the driver circuit heats up, stops output, cools down,
re-enables output, heats up again and so on.
You can also see on the graph that with a dead
short, the output can deliver slightly more than 500mA. So if
all three outputs are shorted, total consumed current is more
than 1.5A, exceeding rating of the fuse
that protects RCX. This condition should not happen in normal
circumstances, even with all three outputs loaded with 2 stalled
71427 motors...
I also had a look to current output capabilities
of 8475 RC
Race Buggy. Its main output drives two paralleled 5292 motors
that consumes more than 3A when stalled so it has to be beefy
! And indeed it seems to have a current limitation of about
4A, and a thermal shutdown providing on/off cycling like RCX
motor driver.
Getting maximum
mechanical power from RCX output
October 2012 update:
Similar curves for Power Functions motors driven by PF IR-receiver
are available here.
Using an illimited power supply (fresh batteries for example),
a DC motor provides maximum mechanical power when loaded at
half of its stall torque. This is also the load where rotating
speed is half of no-load speed (this assumes ideal conditions
such as low internal friction, but according to load curves
showed above, this is exact enough to be useful).
But with RCX output, some voltage drop occur as current increases,
and current limitation can also trigger in if two motors under
heavy load are paralleled on the same output.
Here are the curves showing mechanical power versus load
torque for various motor combinations. The RCX was externally
powered from a regulated power supply, and I measured mechanical
power at 9V (equivalent to 6 alkaline batteries) and 7.2V (6
NiCd or NiMH rechargeable batteries).
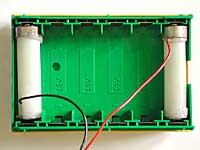
|
RCX powered by an external regulated power supply
through two fake batteries.
Caution: I shall not be held responsible
if you burn your RCX with incorrect voltage or bad
polarity ! |
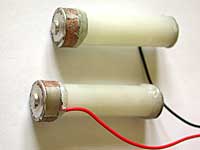
|
The fake batteries where assembled from the sawed
ends of old alkaline batteries, maintained at the
right spacing with rods of hot melting glue.
Caution: batteries contain hazardous
chemicals that can be dangerous for your health.
Open them at your own risk and only if you know
what you are doing!!! |
You can see from the curves that although RCX can be operated
from NiMH batteries, the lower supply voltage translates in
a 40% cut down of available mechanical power .
Single motor curves
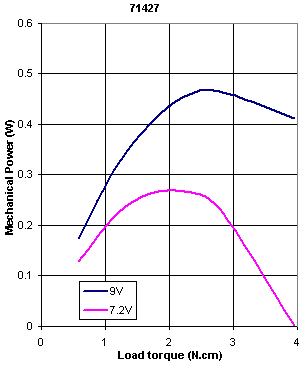
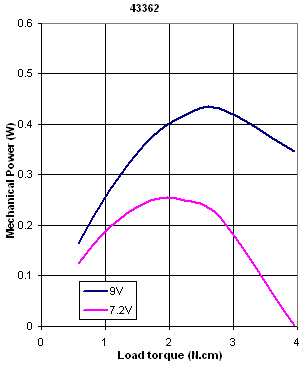
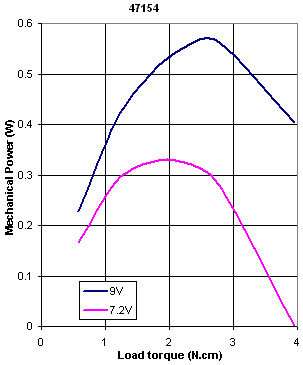

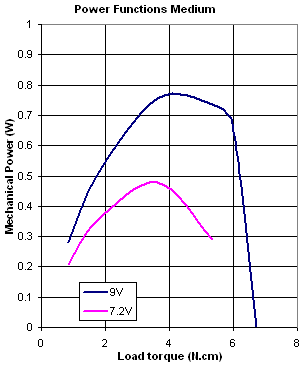
Paralleled motors curves
Two identical motor are powered from the same RCX output,
and their shaft are mechanically coupled.
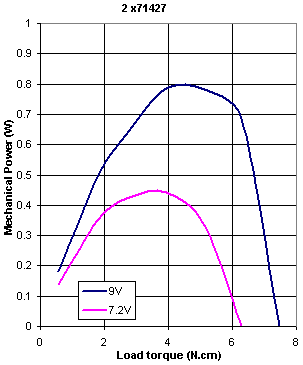
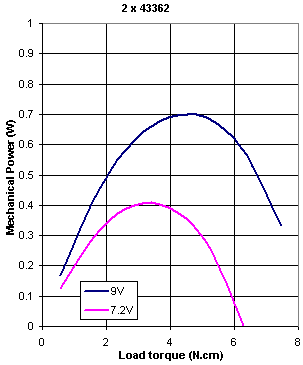
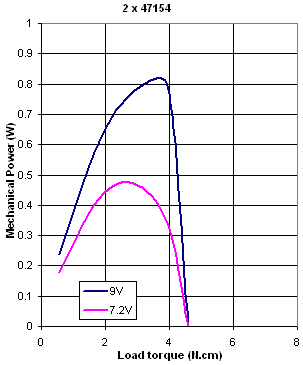
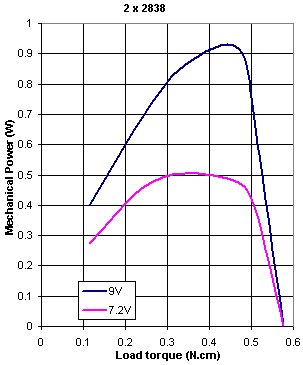
Because of the higher current consumption of
47154 and 2838 motors, using two of them on the same RCX output
is not recommended, as they exceed RCX current limitation when
heavily loaded. At 0.8 W, tandem 71427 provide safely the greatest
mechanical power of all.
Conclusion
Each of these motors has unique characteristics which makes
it more or less suitable for different applications.
- Micromotor 2986 is at its best when space or weight
is at a premium. But its mechanical power is quite low.
- Technic motor 2838 is a real power hog, with poor efficiency,
but it can deliver 30% more power than Minimotor.
- Minimotor 71427 is probably the best performer of the
pack overall.
- The new 43362 is roughly equivalent to 71427, with slightly
degraded performances. But its light weight can be a boon
for many uses.
- Clear case 47154 provides a higher mechanical power
than 71427, but at the price of a somewhat lower efficiency.
- RC Race Buggy Motor 5292 is really powerful, but requires
a power supply up to the task. It's not a good idea to use
it with a RCX as the 500 mA current limitation won't let
it unleash its power...
- NXT motor delivers a high torque thanks to its internal
speed reduction gear train. Because of that, it also turns
slowly and efficiency is somewhat reduced. This motor could
be connected to RCX thanks to a compatibility cable, but
this is not recommended for use on a RCX because the high
current it can consume is too much for RCX 500 mA current
limitation.
- The Power Functions train motor has widely improved
characteristics compared to the older RC train motor.
Caution
! Though I tested motors with a 12V supply,
I can't guarantee that they bear the extra load
for extended time period. Use that
at your own risks ! |