|
|
Cuckoo
Clock
November
2013 update: Daniel Weissengruber
created a LDraw file with building
steps using my photos. Anybody should
be able to rebuild this clock -
note that I have not thoroughly
verified the file, but it certainly
looks like a great job - Many thanks,
Daniel!
|
|
In March 2011, the French LEGO
Technic forum SeTechnic launched a competition: build
a purely mechanical cuckoo clock out of LEGO pieces. The
target was to build a clock able to work at least 30 seconds,
and in the end have a cuckoo bird going out...
Evaluation criteria:
Clock running time (for those using
weight, their maximum travel was fixed to 50cm)
Proper ratio between seconds hand
and minutes hand
Hour hand with correct ratio
Quality of cuckoo mechanism
Aesthetics of the clock and cuckoo
Originality of mechanisms and techniques
used
As building a clock is something I considered for a long
time, I decided to participate. The description below is more
or less the translation of the text of my submission, describing
the design process.
I was lucky enough to win the competition, despite many other
valuable entries ;)
LDraw/MLCad
file

|
Daniel Weissengruber-
FLY(at)gmx(dot)at - created a LDraw file with building
steps using my photos - Many thanks, Daniel!
Download the LDraw/MLCad MPD file. |
Videos
Photos
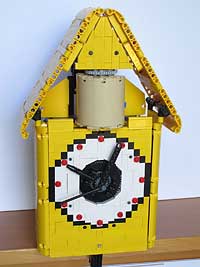
|
Close-up of the whole clock. |
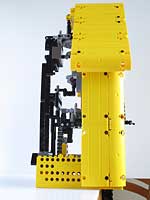
|
Side view. I didn't have enough panels
to completely close the box. The good point is that
it shows the mechanisms! |
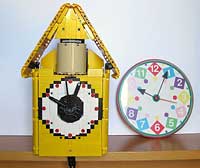
|
Near reference clock. As you can
see on the first video, cuckoo clock speed closely
matches real clock one. |
Construction
details
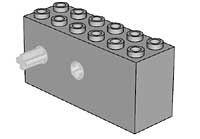
|
The first choice I had to do was
to select the power source of the clock. Using weight
is a classical method, but I like a lot the small
wind-up motors 42073, and ended up using
two of them, one for the clock itself, the second
one to power the cuckoo. |
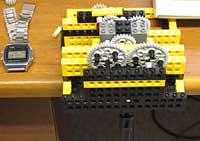
|
But I was not yet sure this little
motor could power the clock long enough. I quickly
assembled it on a W4.3 de Ben Van De Waal escapement,
and easily got a 2 minutes running time, with direct
connection of motor output to escapement.
As the motor had power to spare, I multiplied
by three the motor output (24t:8t) and obtained
6 minutes running time. It would probably be possible
to go further in multiplication to get a longer
working time... |
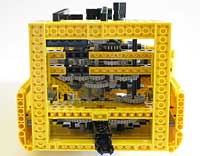
|
As the Ben Van De Waal's escapement
worked fine, was simple, compact and easy to integrate,
I used it for my clock. The test structure, a bit
improved, became the clock chassis, as can be seen
on this bottom view photo. |
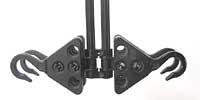
|
The pendulum itself is built from
long Technic axles and 4 metal crane hooks as weight.
I find it looked nice... The weight can be easily
slid up and down to trim pendulum period. |
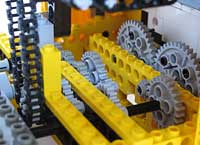
|
The escapement makes one turn every
4 pendulum periods, that is to say every 5 seconds
(8 x 0.625s). This means that I needed to divide
by twelve to drive seconds hand. Since the motor
output is multiplied by 3 to drive the escapement,
taking directly the motor output it only remained
to divide by 4. This was done with two 8t:16t gears.
The divided output is provided to the dial driver
module with a chain. |
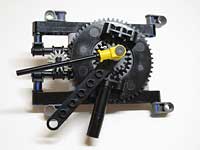
|
The next module I built is the dial
that features three concentric hands. Seconds hand
is directly driven by central axle, while hours
hand is mounted on the crown of a turntable. |
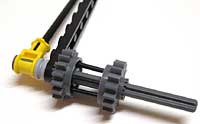
|
Minutes hand is driven by two head
to head 6542
gears, assembled with four 4593
control sticks. It's a bit tricky to assemble,
and transmitted torque is not outstanding (though
stronger than I first expected). But it allows to
directly use a Technic plate as minutes hand, and
total handle stack height is just 3 studs. |
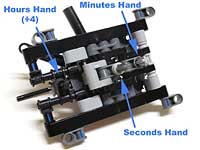
|
Backside of the dial module. Hours
input is divided by 4 (14t:56t), the dial driver
module will only do a simple divide by 3 between
minutes and hours. |
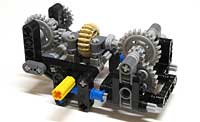
|
The next module I built was the dial
driver module, ensuring proper divisions between
hours, minutes and seconds. |
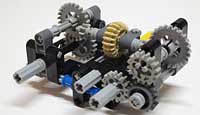
|
Since the needed transmitted torque
is fairly low, I used twice a floating assembly
on axles to get non-standard spacing. This allowed
to use a worm screw on a 20t gear (followed by 8t:24t)
to get the proper divide by sixty between seconds
and minutes. This setup is very compact. Non-standard
spacing was used also to compensate for the odd
distance caused by the use of 14t gear for hours
in the dial. |
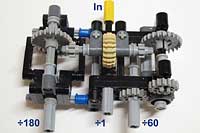
|
Driver module, showing division ratio. |
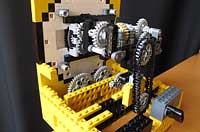
|
The next step before building the
cuckoo mechanism was to assemble all these modules
and check the result. It's also at this step that
I added a reasonably nice dial background. Noteworthy
is the weight brick that is supposed to prevent
clock tipping. "Supposed to" because I
drop the clock twice during video shooting! |
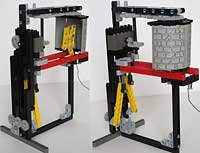
|
Here is the prototype of the cuckoo.
The wind-up motor drives the half cylinder that
hides the cuckoo in rest position. When the cuckoo
is triggered, the cylinder turns and shows the cuckoo,
while a thread gets taught and pulls the lever of
scissors mechanism that raises and pulls out the
cuckoo. The weight of the cuckoo allows it to go
back inside cylinder footprint as soon as the thread
is loosen. A double bar interlock mechanism allows
to block the rotation and to release the cuckoo
only once per cycle. The axles easily slide on the
cuckoo lever, so the clock mechanism is not hampered
by friction. |
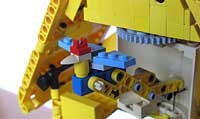
|
Cuckoo! cuckoo!
While this mechanism worked quite well, the motor
is missing a bit of torque, sometimes failing to
lift the cuckoo. I guess I should have used more
down gearing on motor output (1:3 here). The other
drawback is that as the cuckoo turns, the thread
gets more and more twisted, slightly shortening.
So you have to adjust its length from time to time... |
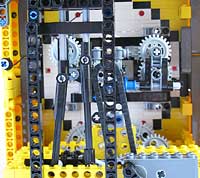
|
It only remained to add cuckoo mechanism
to the clock, and cover it with a few panels. This
photo shows the cuckoo release mechanism after integration.
On the left you can also see the thread bobbin,
used to adjust the tension. |
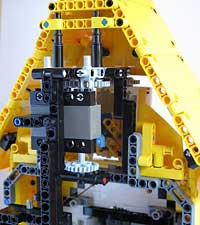
|
The wind-up motor driving the cuckoo.
We can see this one folded down in the back. |
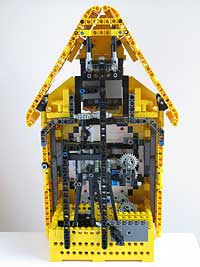
|
Complete view of the back of the
clock. |
|