NXT® motor internals
February
2007 update: Ryo Watanabe computed NXT motor constants
from the curves below, as well as from his own measurements.
Read more here.
March 2008
update: Kevin Knuth of BrickEngineer
experimentally determined the center
of mass of NXT motor.
November
2008 update: Daniele
Benedettelli sent me photos of a fully open broken NXT motor.
See bottom of this page.
December
2020 update: RocGravillon sent me photos and procedure
to properly open NXT motor without breaking hub. See here.
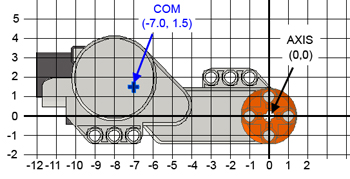
NXT
motor characteristics
9V motors
comparison page shows some characteristics of this motor
considered as a 9V motor, but here are some more information
on its use with a NXT (its main use!!!)
The curves below shows NXT motor rotation speed
(Rotations per Minute) vs. motor power level (supply duty cycle).
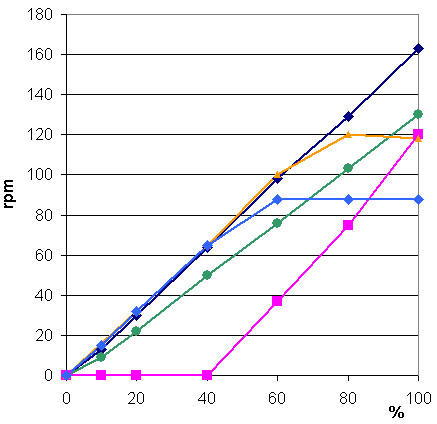
|
Motor not loaded, 9V NXT power. Most noticeable
here is the linear relationship between power level
and motor speed. Much more practical than what we
got with RCX where unloaded motor ran almost full
speed at power level 2. Since there is no load to
overcome, Power Control would have no effect here.
|
Motor not loaded, but this time the NXT is powered
at 7.2V (what you get with NiMH batteries). Of course,
rotation speed is proportionally lower.
|
Motor behaviour with a 11.5 N.cm load applied, no
Power Control, 9V NXT power. Below 40% motor is
stalled (horizontal region of the curve). Once enough
power is applied, speed increases proportionally.
|
Motor loaded with a 11.5 N.cm, 9V NXT power. This
curve shows the efficiency of Power Control: up
to 70% the speed is the same as an unloaded motor.
After that the curve is flat, the motor is actually
running at full power. Note that motion as 10% was
very irregular, even if average rpm is OK.
|
Motor loaded with a 11.5 N.cm, 7.2V NXT power. Up
to 50% the speed is the same as a no-load, 9V powered
motor (and actually faster than a 7.2V powered motor
without Power Control!). The plateau appears at
a lower duty cycle, since there is less energy available.
|
The following charts show the characteristics of the NXT
motor versus applied load. For the dark blue curves, the NXT
was powered at 9V (voltage of alkaline batteries), the magenta
ones were obtained at 7.2V (voltage of NiMH batteries). Power
level is 100% for all charts.
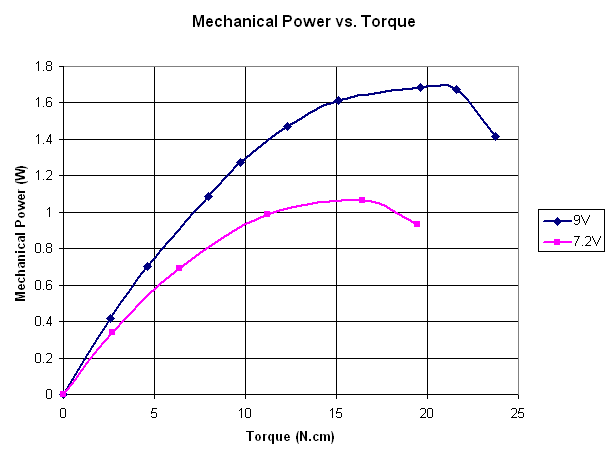
This curve shows that the maximum mechanical power is obtained
at a torque load of about 15 N.cm. If you compare to the curves
obtained for the RCX with 71427 motor, you see that the
available mechanical power is much higher, almost 4 times! Even
powered with 7.2V NiMH batteries, the NXT can deliver more power
than a RCX output with 2 paralleled motors and 9V supply. This
comes with a price of course, the current drained at that power
level is much higher - you better have good batteries...
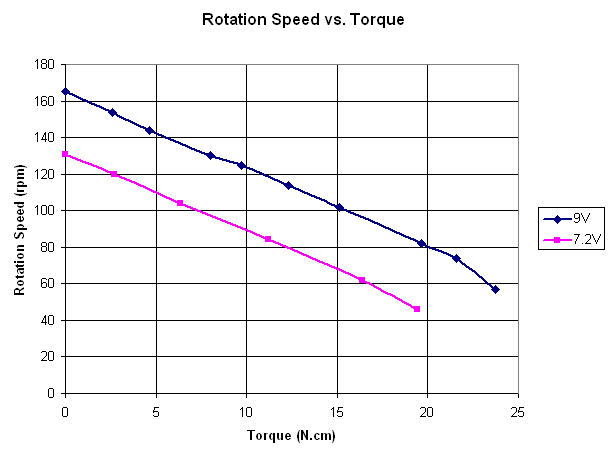
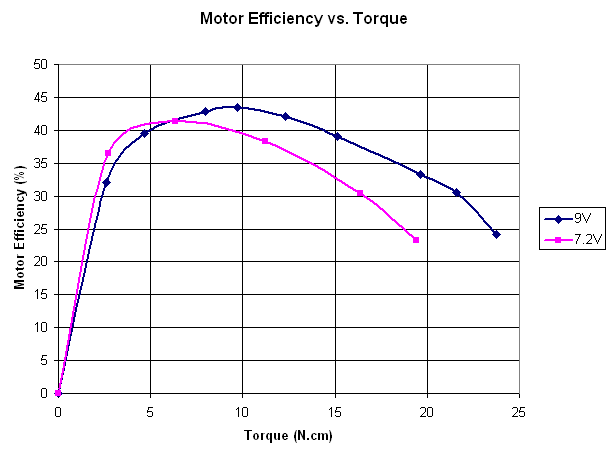
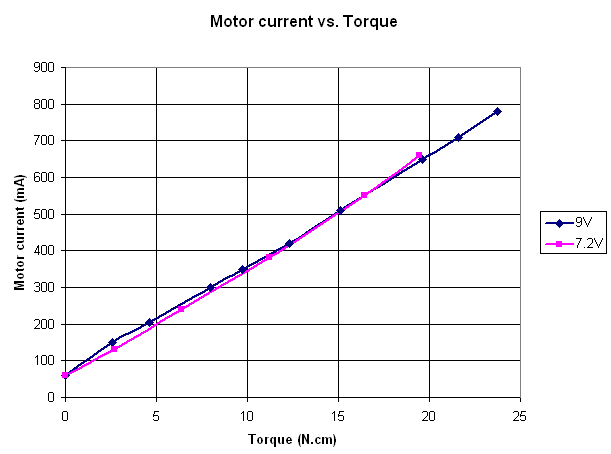
The current vs. torque shows a linear increase with the load.
Because of power limitations in NXT driver, and thermistor trip
current in NXT motor, I suggest that you don't exceed a 15 N.cm
torque for extended time periods. Higher loads (thus current
drains) are possible for short periods, but the protections
will soon reduce current and available power.
Photo
Gallery
The cool drawing at the top of this page shows
many things, but nothing beats seeing the real thing. So I opened
one of my motors and took some photographs...
Warning: Separating the orange shaft
parts is impossible without breaking things. Don't try that!
Also notice that reassembling the motor partially opened as
I did can be tricky!
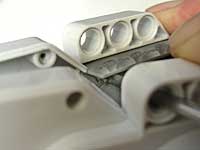
|
Once you have removed all seven screws
visible outside (using a thin Torx T5 screwdriver),
there is an eighth one to be removed inside... You
can access it by flexing the plastic motor case. |
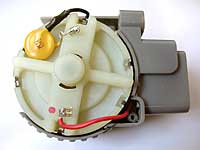
|
When all screws are removed, you
can slide the motor assembly out of its case. |
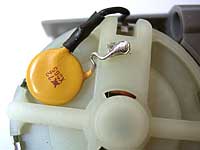
|
The yellow component is a resettable
fuse that protects the motor and the NXT from over-currents.
It's a Raychem RXE065
or Bourns MF-R065. |
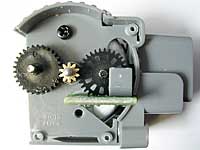
|
The other side of the motor shows
the encoder wheel and optical fork that provide
rotation sensor function to the NXT motor. |
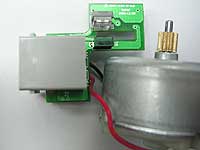
|
The motor and printed circuit board
bearing motor connector and optical encoder. |
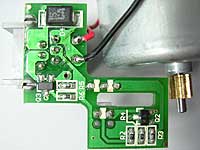
|
Bottom of the PCB, mainly used for
optical encoder signal conditioning. The black rectangular
component on top is a surge suppressor that clamps
voltages to 15 volts maximum. |
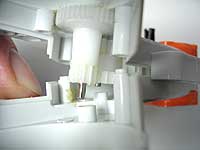
|
You may also have a glimpse on the
gear train. Unfortunately, since the orange shaft
parts can't be separated, we can't go further. |
Here below are some photos of a broken
NXT motor, fully open. Photos courtesy of Daniele
Benedettelli.
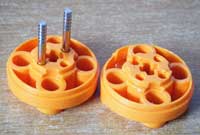
|
Output shaft of the motor broke under
load! This photo also shows the asymmetric ribs
on the metal pins explaining why it is impossible
to disassemble the hub without breaking it. |
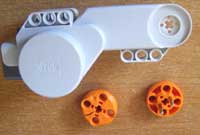
|
Motor hub and casing. |
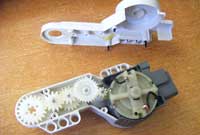
|
Photo showing motor inside. |
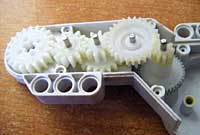
|
Close-up on the gear train. From
motor to output shaft, we get these gear ratio:
10:30:40 = 1:4
9:27 = 1:3
10:20 = 1:2
10:13:20 = 1:2
Overall 1:48
|
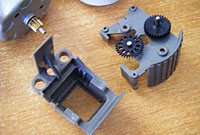
|
Encoder wheel and enclosure back
parts. We have 12 slits in encoder, and motor to
encoder gear reduction is 10:32. So for 1 turn of
output hub, encoders turns 48*10/32=15 turns, optical
detectors sees 15*12=180 slits. Using both sides
of slits gives nominal 360 ticks per turn resolution.
Note that since we have a quadrature encoder, the
maximum resolution is 720 ticks/turn, but this is
not used by standard NXT firmware. |
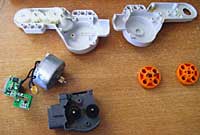
|
Exploded view of the motor. |